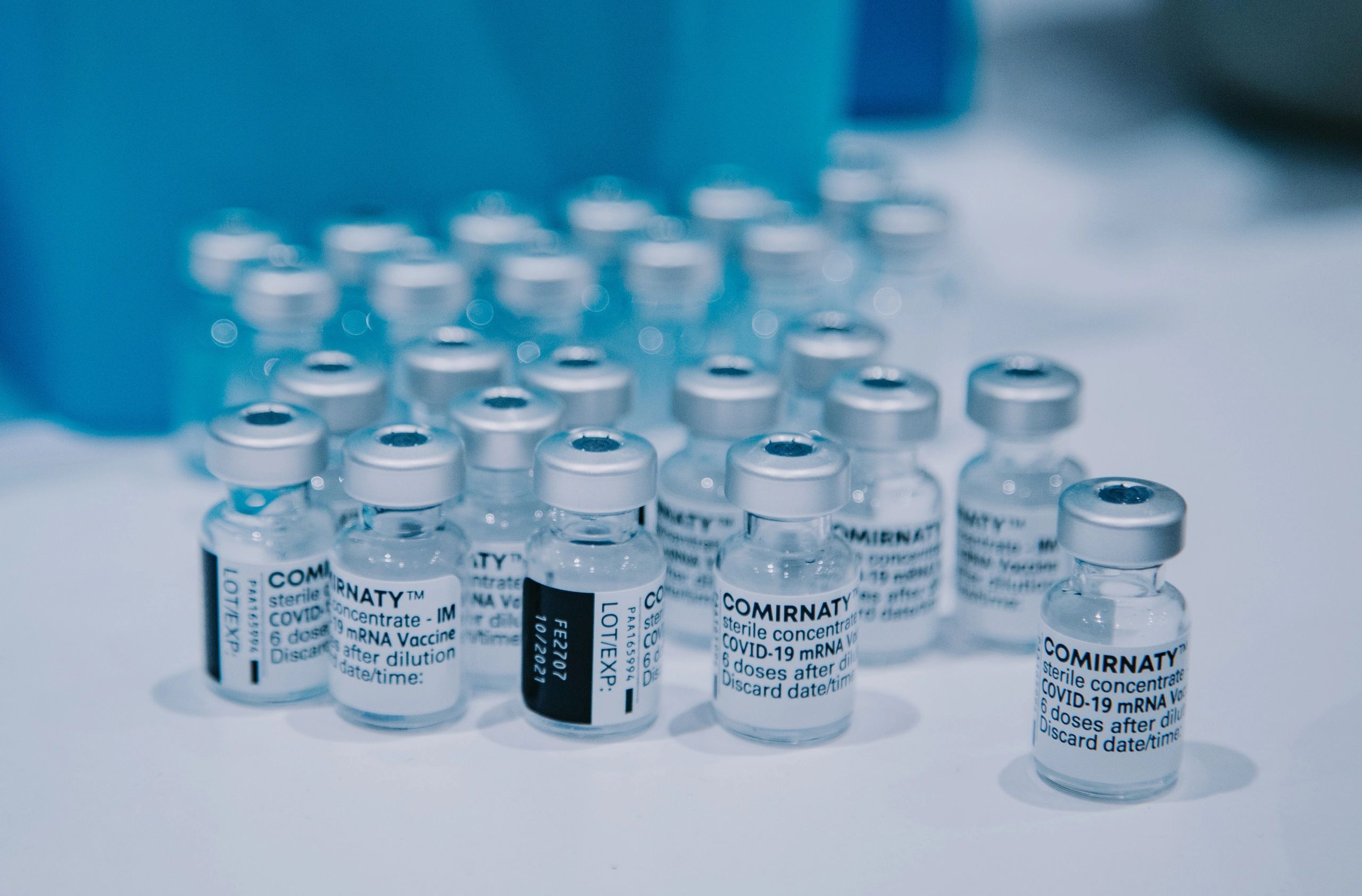
I’ve been working on talent development projects since 2018. Still, this effort kicked into a higher gear in 2020 when we received a grant to develop a Bioscience Career Launch program in our regional high schools. I’ve learned much from my colleagues and our experiences in these projects. However, the most important lesson is that we can’t continue doing the same things and expect an increase in qualified candidates for biomanufacturing and life science roles. I share my thoughts on how to address the challenge in this article. Follow me if you’d like to learn more or join the awareness campaign!
Companies engaged in current Good Manufacturing Practice (cGMP) manufacture of drugs, vaccines, biologics, and medical devices are experiencing an urgent need for employees. This need existed before the pandemic and has only intensified in the wake of the attendant economic and workplace upheaval and the global social and racial justice movements. Ensuring a safe and reliable supply of critical medicines is a national security and biodefense concern. The US government and many companies are investing to increase biomanufacturing capacity in the Americas. More and expanded facilities mean even more workers will be needed. How can we address the current and future demand for the cGMP workforce? I’ll share some practical ideas from work I’ve done with colleagues as an adjunct faculty member at Washington State University (WSU).
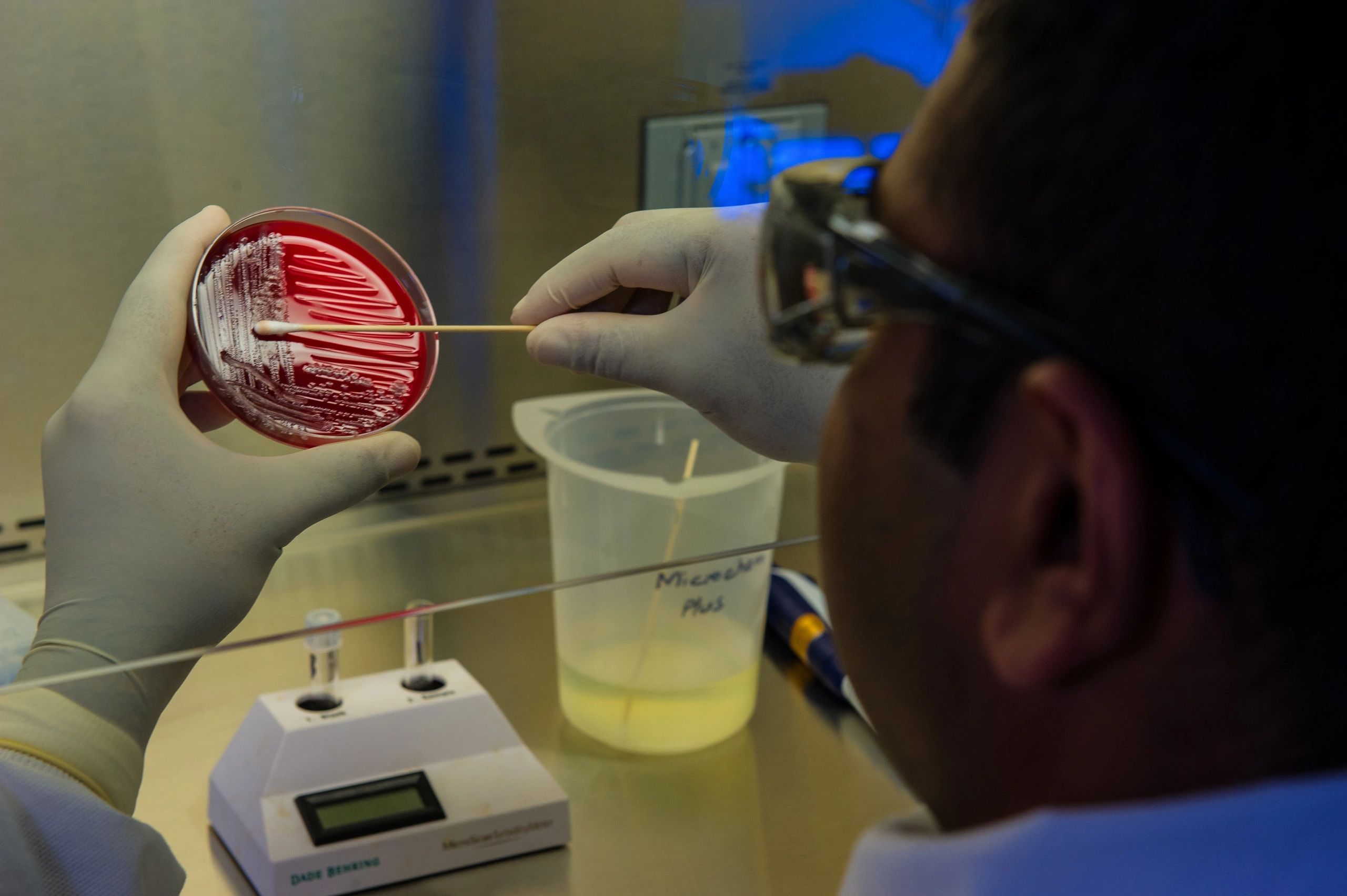
First, what do the regulations say about the personnel qualifications needed for cGMP manufacturing? From 21CFR Part 211.25, these are:
a) Each person engaged in the manufacture, processing, packing, or holding of a drug product shall have education, training, and experience, or any combination thereof, to enable that person to perform the assigned functions. Training shall be in the particular operations that the employee performs and in current good manufacturing practice (including the current good manufacturing practice regulations in this chapter and written procedures required by these regulations) as they relate to the employee’s functions. Training in current good manufacturing practice shall be conducted by qualified individuals on a continuing basis and with sufficient frequency to assure that employees remain familiar with CGMP requirements applicable to them.
b) Each person responsible for supervising the manufacture, processing, packing, or holding of a drug product shall have the education, training, and experience, or any combination thereof, to perform assigned functions in such a manner as to provide assurance that the drug product has the safety, identity, strength, quality, and purity that it purports or is represented to possess.
c) There shall be an adequate number of qualified personnel to perform and supervise the manufacture, processing, packing, or holding of each drug product.
The bold text is my addition. The regulation declares no specific degree requirements for any position. It calls only for a combination of education, training, and experience appropriate for the assigned functions. Inspectors expect you to demonstrate through your policy, program, and process documentation that an individual employee is qualified for their particular role. Since every company mandates initial and ongoing training in their SOPs, we can consider how education and experience criteria contribute to identifying candidates.
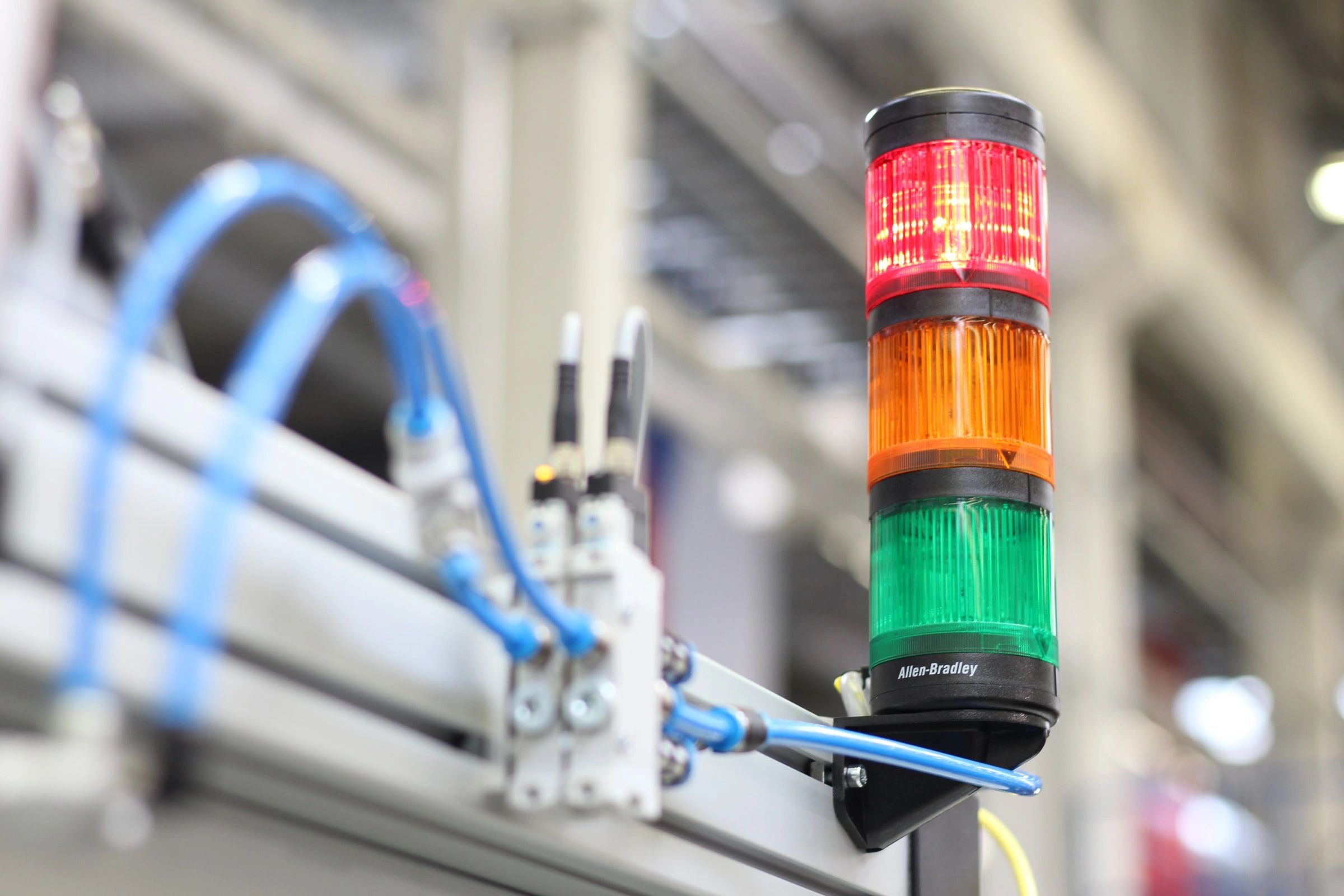
What kind of education and experience is needed? The Coalition of State Bioscience Institutes (CSBI) released a helpful report on life sciences workforce trends in June 2021 that we can use as a starting point. I’ll note that this report relies on data from job postings from 2016-2020 and a hiring survey and executive interviews that were conducted in early 2021. Therefore, the report incorporates some, but not all, of the pandemic-related trends. In addition, the results cover the full range of life science roles and companies so that they will under-represent cGMP medical product manufacturing. Nevertheless, it’s a good and recent source for the bioscience industry’s position on their workforce.
The report confirms the life sciences sector’s essential role and recession-resistant nature during 2019-2020. Hiring in the industry increased by 1.4% during this period when, at the same time, total private-sector hiring decreased by 5.1%. Eighty-four percent of the job postings were in the pharmaceutical, medical device, and research testing/medical lab sectors, again pointing to the essential role of this industry in pandemic response. The sector employs a more highly skilled workforce emphasizing science, technology, engineering, and math (STEM) skills compared with all industries. While life sciences are science and engineering-based industries, there is a significant demand for talent in managerial, financial, sales, IT, and other business functions. While nearly half the roles call for a postsecondary degree, at least one in three industry jobs are positions for a skilled technical workforce, filled by persons with “STEM skills and knowledge who do not have a bachelor’s degree.”(1) More and more, life science companies are partnering with community colleges and K-12 schools to help develop more candidates with biotechnical skills. NSF supports these programs through InnovATEBIO, the National Biotechnology Training Center. Regional programs also partner with K-12 schools in areas commonly associated with biotech, like New England and North Carolina.
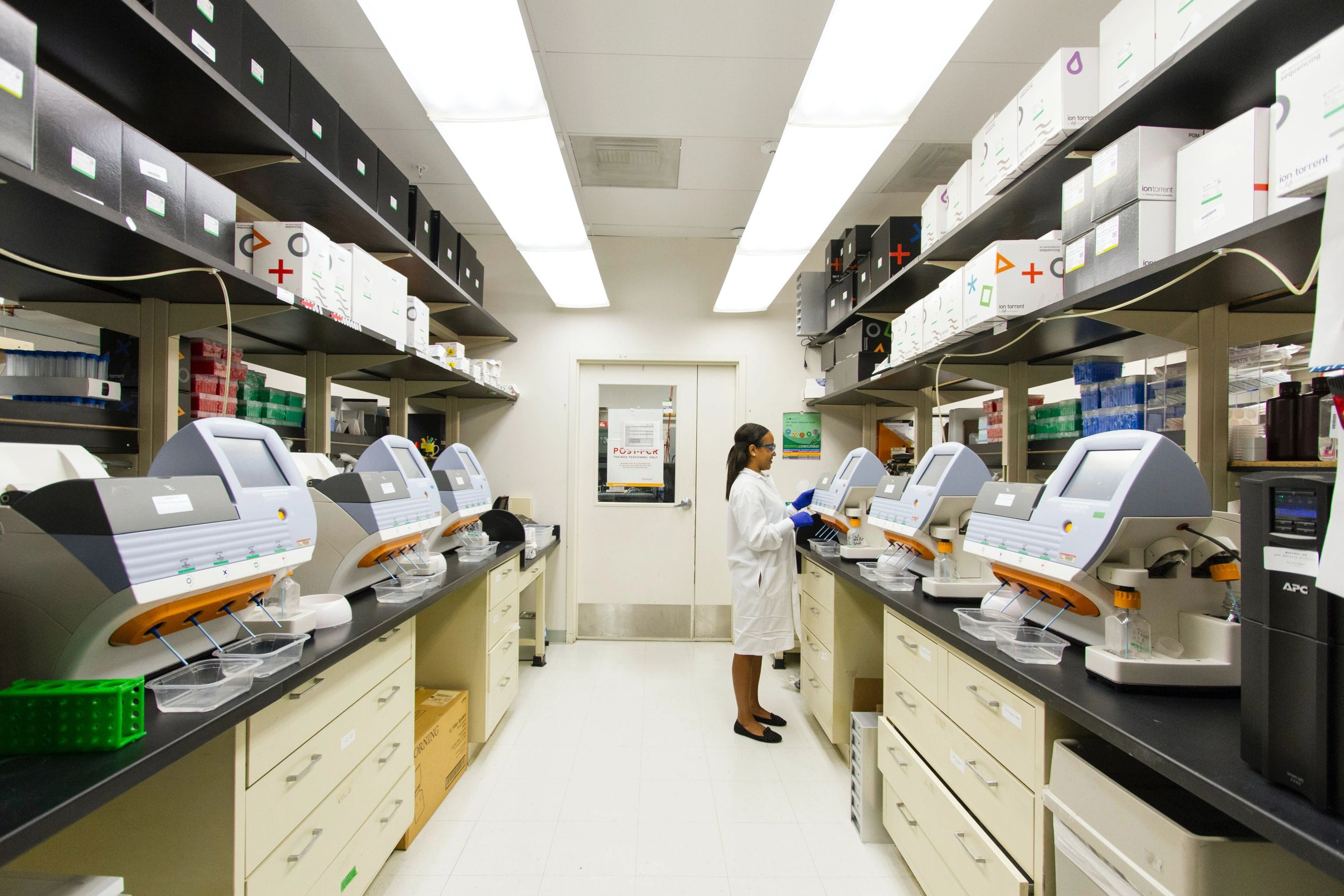
I argue that every role in biomanufacturing has been and can be performed by persons with a high school degree and training. Furthermore, the report shows the industry is already shifting to value experience as much as a degree. Once we adopt this viewpoint, it’s not a leap to see that three categories of solutions to the talent capacity challenge exist now. Undoubtedly, many will argue that we need more training programs; however, these are just one piece of the puzzle and necessarily a longer-term fix. Even shortened training programs can be too long when companies face an urgent worker shortfall. Instead, let’s look at approaches that can start adding to the candidate pool now, including expanding industry awareness and finding candidates where they live. Then we can create better pathways into and within our companies through training and education programs. Let’s look at each solution individually.
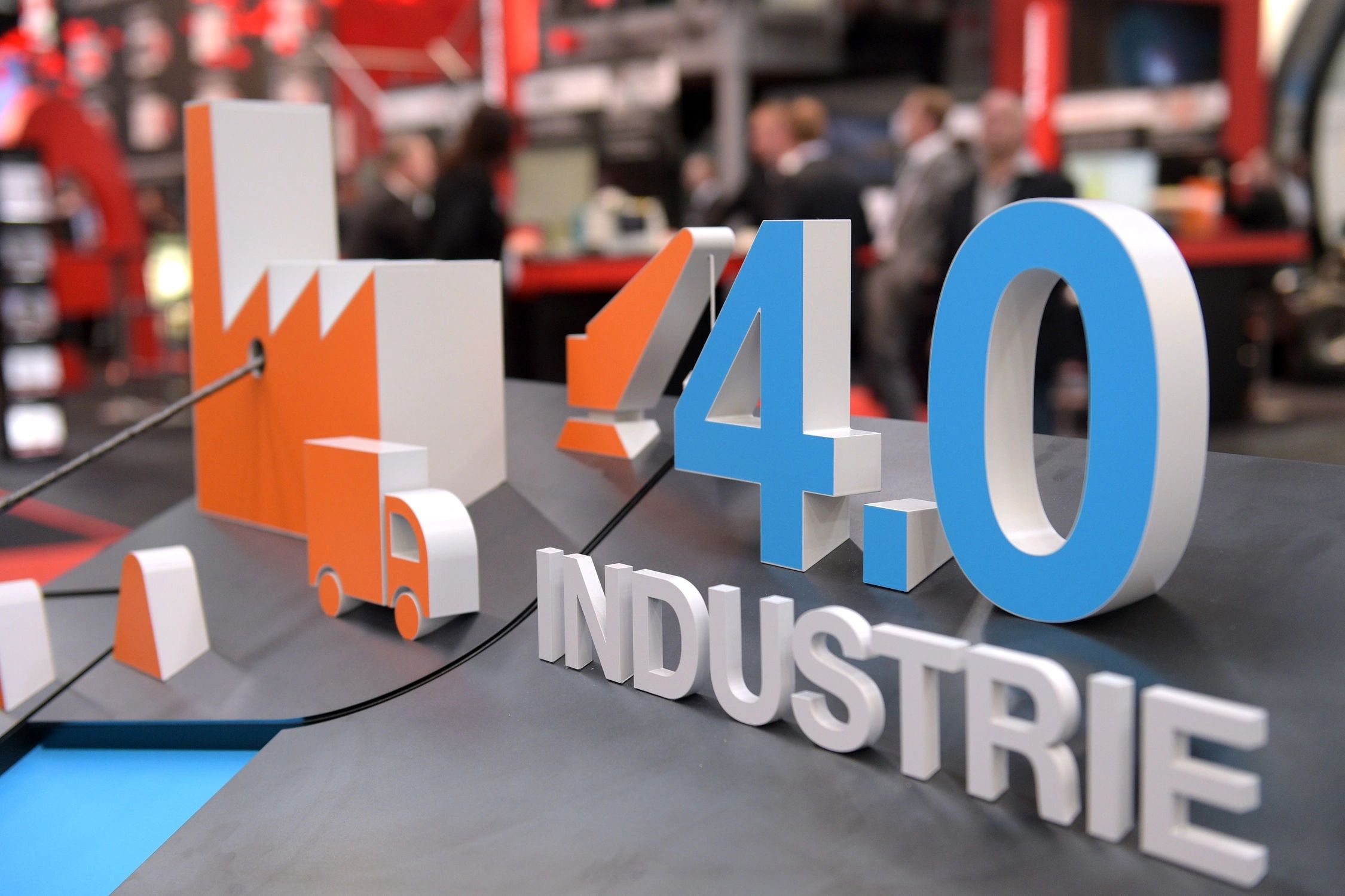
Expanding Industry Awareness
The pandemic has familiarized the public with some scenes of biomanufacturing, like vaccine vials exiting a capper or aggregating into a collecting area for trayoff. We’ve also seen a few people in the classic “bunny suit” of full aseptic gowning. Nevertheless, I repeatedly find that students, parents, faculty, and community members are unaware of the types and quantity of biomanufacturing jobs available. This awareness gap occurs even with large and growing facilities within their city. The term “manufacturing” also triggers inaccurate perceptions of the work, failing to recognize the STEM nature of the work and the increasing automation, computers, and technological advances in the life sciences. On the flip side, many think of life sciences only from the research angle. This view fails to recognize the much larger effort and facilities needed to commercialize a medical product. It also directs people to think a degree is required to work in life sciences, a point we have already refuted above.
A concerted campaign by industry, aided by government and academic partners, is essential to reveal the full benefits and adjust perceptions of biomanufacturing. National, regional, and local media elements that showcase actual workers performing their tasks and sharing experiences can have a powerful impact. Your local public television and radio stations can play a part. One award-winning example is the Career Explore NW program by PBS station KSPS in Spokane, WA. This career spotlight for Environment Monitoring Technician filmed at aseptic fill-finish manufacturer Jubilant HollisterStier offers a peek into a critical function in creating sterile medicines. Companies should also recognize how valuable employees are as ambassadors by creating work assignments on company time to visit schools, colleges, job fairs, and other events to share their roles and the importance of STEM skills to the industry. Armed with suitable supporting materials and social media links, they can easily share the many opportunities currently available for the skilled technical workforce in your company. I find engaging with students in this way renews my excitement about the industry.
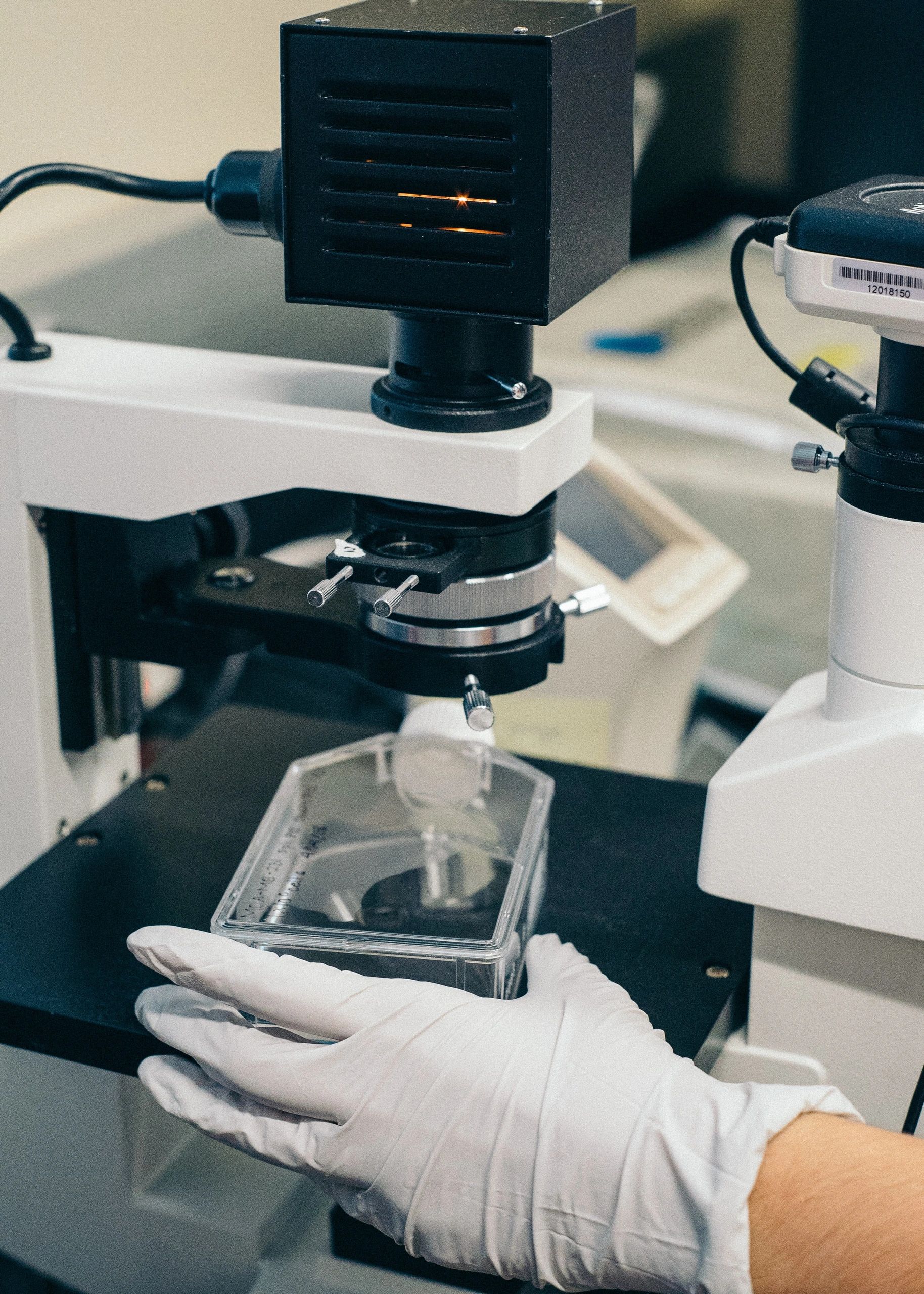
Finding Candidates Where They Live
Triggering excitement in the community about your opportunities should bring renewed interest in your company and an increase in applications. However, applying your standard hiring requirements to this new candidate pool will leave your managers overwhelmed and as frustrated as they were with too few candidates. Consistent with the findings of the CSBI report, it’s important to start adjusting your expectations for education and experience in each position. Undoubtedly, this will take a concerted effort to rethink job descriptions and retool hiring processes. However, our industry has proven capable of rapid innovation under challenging paradigms, and this is an opportunity to engage your current team in thoughtful conversations across all levels.
Graduates of high school Career and Technical Education (CTE) programs are a relevant and frequently overlooked source of life science talent. Notably, these are not the CTE or vocational education programs you may have experienced in your secondary education. The latest reauthorization of the federal Career and Technical Education Act (known as Perkins V) expanded the requirements for CTE funding to include programs of study leading to an industry-recognized credential, dual credit, and paid work experience. A state-provided career exploration program for K-12 students is another requirement. In Washington State, this is the Career Connect WA program, which also receives state funding. Schools have responded by reworking their CTE programs, often with the help of nationally recognized providers of STEM curriculum like Project Lead The Way (PLTW). Biomedical science CTE programs offer experiential learning focused on developing STEM and transferable skills through realistic projects requiring team-based research, lab work, and written and oral presentations. Students passing the exam to earn a bioscience industry-recognized credential like the Biotechnician Assistant Credentialing Exam (the BACE) have demonstrated the knowledge and practical skills required for entry-level roles. Thus, that credential has value as a preferential criterion in hiring decisions. Other CTE programs (like those for computer science and engineering) have graduates with valuable skills and STEM knowledge. These students may be preparing for post-secondary education, but many are looking for career-relevant employment to fund their education or expand their resumes. Focusing some of your employee engagement and marketing efforts on students in K-12 CTE programs is a quick way of attracting candidates with proven STEM aptitude.
Finding your candidates in place also means putting effort into making your company more attractive to your existing employees. First, redesign your benefits programs to reduce friction for your workers and increase community engagement. Adding additional support like transportation, child care, and finding perks like special discounts and services from local providers are all options. Your workers will be happy to suggest other innovations. In addition, show your employees you value their knowledge and experience by offering temporary and rotating assignments in different units to develop their intra-company network and team skills and prepare them for future promotions. Lastly, work with local post-secondary institutions to update your development programs to include more pathways to advanced training and degree completion. Such routes include receiving transcript college credit for earned experience, part-time associate’s and bachelor’s degree programs, and flexible work hours to facilitate coursework. Improving your employee support systems will also contribute to the impact of your public awareness effort since satisfied employees will be your best spokespersons.
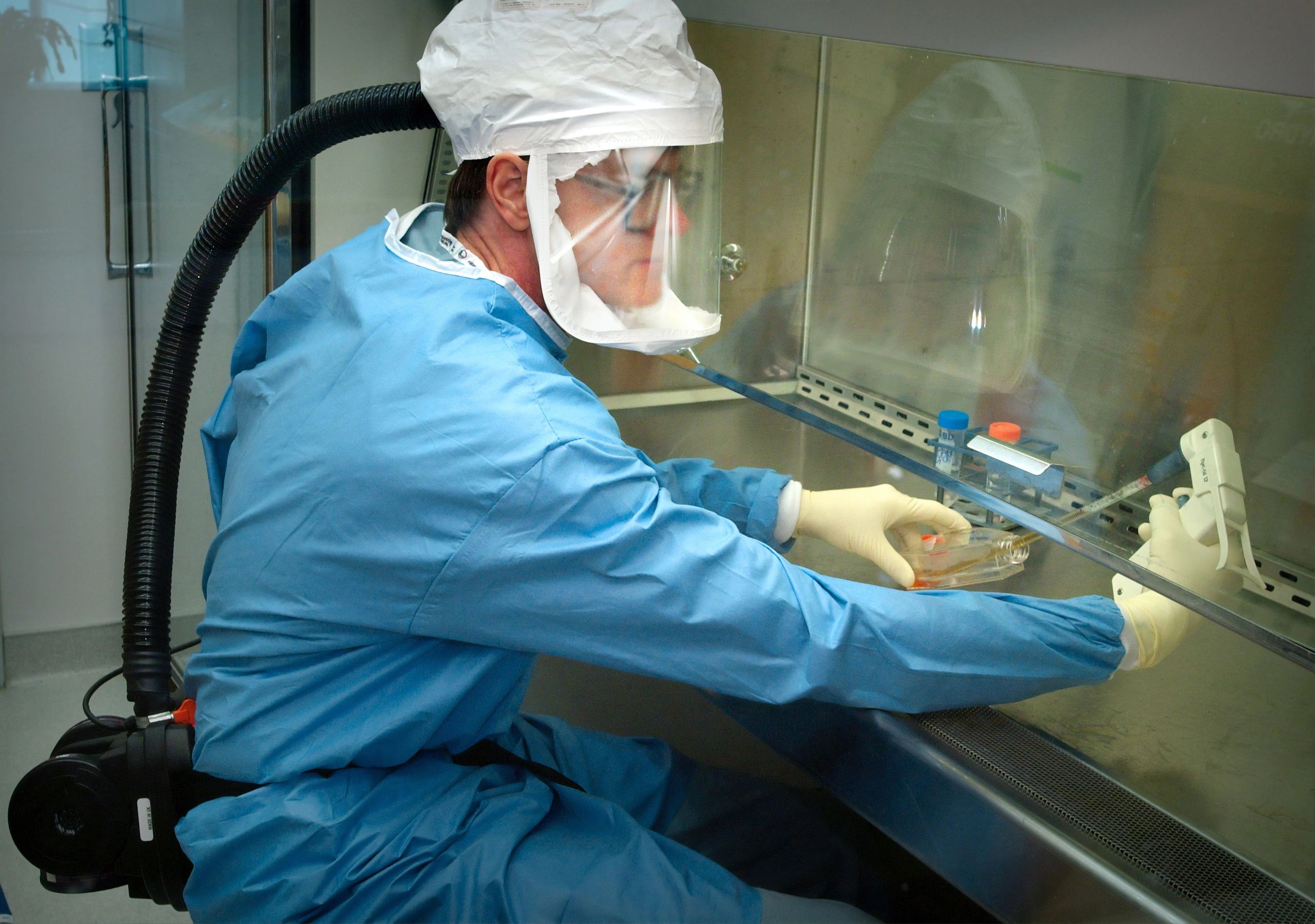
Creating Better Pathways
Establishing local training programs takes longer but is essential to address the future demand for bioscience talent. The knowledge, skills, and aptitudes these workers need will remain STEM-focused; however, we can expect changes due to the highly innovative nature of the industry. Let’s recall that experts in an Institute for the Future expert workshop in 2017 predicted that “eighty-five percent of the jobs that today’s learners will be doing in 2030 haven’t been invented yet.”(2) The diversity initiatives that many companies established after the social upheaval of 2020 depend on applications from a broader set of candidates. These include persons historically underrepresented in post-secondary programs, under-employed adults, and those shifting from transforming industries. In addition, your existing employees seek ways to increase their capacity and often ask for appropriate training in areas of need.
CTE training is historically associated with the nation’s community and technical colleges. If your local college does not have a bioscience training and degree program, They can engage with the federal InnovATE BIO initiative to get started. However, these programs will not take root or offer the most valuable curriculum without active engagement by local company employees. Therefore, companies should work holistically to fit these programs into their re-vamped employee development frameworks. That means sharing details of your role requirements and working with college administrators to develop the learning frameworks appropriate for entry-level and more advanced candidates. The college can connect its program to local K-12 biomedical science CTE programs via dual credit for the end of course or credential exams. Additionally, you should connect with four-year colleges and universities to offer pathways to higher degrees and continuing education in STEM and business-critical functions.
In this article, I’ve shared some of the points I’ve learned in talent development work with colleagues at WSU. The road to resolving the workforce shortage in biomanufacturing starts with re-thinking the criteria for candidates. Next comes improving the public perception of the bioscience industry and manufacturing. Next, a considerable internal effort will be needed to think differently about secondary school graduates and existing employees as candidates for current and evolving positions. Lastly, while critical for long-term success, training programs will founder without active industry direction and participation. Finally, I’ll leave you with the thought that talent development is essentially a pre-competitive activity. Cooperating with local companies to benchmark best practices, create development opportunities, and build regional training options will foster a larger ecosystem and help you be more competitive. Before long, you might even find yourself in the middle of a growing innovation cluster!

I’d like to thank my colleagues Diane Lashinsky and Gregg Godsey for our work on the Career Connect Washington/WSU/PLTW Bioscience Career Launch intermediary program grants. I’m also privileged to work with the Flexible Infrastructure for Resilient Entrepreneurship (FIRE) team (Michaele Armstrong, Glenn Prestwich, Brian Kraft, Laurie Donnell, and Jessy Arter) and the Workforce Innovation Network Development (WIND) Advisory board on talent development under EDA Project No. ED21HDQ3070058.
References
(1) Helwig, R., & Letter, D. (2021). 2021 Life Sciences Workforce Trends Report: Taking Stock of Industry Talent Dynamics Following a Disruptive Year. Retrieved from https://www.csbioinstitutes.org/workforce-development
(2) Institute for the Future (2018). The Next Era of Human/Machine Partnerships. Retrieved from https://www.iftf.org/future-now/article-detail/realizing-2030-dell-technologies-research-explores-the-next-era-of-human-machine-partnerships/
If you enjoyed this article and would like to read more by Katrina, sign up for her newsletter.